High Temperature Material Processing
Utilizing high-temp furnace technology to process advanced materials
Brakes
Industrial Coatings
Thermal Protection
Fuel Cells
Hypersonics
Batteries
Semiconductors
Electrolyzers
Industries Served
BAM specializes in materials such as Carbon/Carbon, Silicon Carbide, and Boron Nitride, which are essential for a wide range of industries. Our proprietary technology and state-of-the-art high-temperature furnace systems enable us to deliver the highest quality and most reliable solutions for our customers. At BAM, we take pride in our commitment to innovation, quality, and customer satisfaction to help you achieve your goals.
Aircraft
Brakes for commercial and military aircraft
Automotive
High performance carbon-ceramic brakes for specialty vehicles and ultra performance race cars like Formula 1
Space & Defense
Thermal protection systems for hypersonic missiles, aircraft, and rocket launch vehicles
Semiconductor
Carbonization and pyrolysis of carbon materials in semiconductor equipment to make chips
Energy
Graphitized carbon to coat components to improve electrical conductivity for EV Batteries, fuel cells, and electrolyzers
Capabilities
BAM is a leading-edge advanced materials company that specializes in the development and utilization of our revolutionary, proprietary technology in high-temperature furnace systems for the processing and manufacturing of carbon solutions. Our cutting-edge technology enables us to provide a range of services. Click below to see details of our process.
We pride ourselves on delivering exceptional quality in all of our carbon solutions, which are used in a wide range of applications. Our team of experienced engineers and technicians utilizes the latest manufacturing techniques to ensure that our products meet the highest standards of quality and precision. From the initial design phase to the final product, we work closely with our clients to ensure that their specific needs are met and that they receive the best possible carbon solutions for their unique, high temperature applications.
Advanced Materials
- Carbon, Carbon/Carbon, Graphite
- Ceramics, Silicon Carbide, Boron Carbide and Boron Nitride
- Powders
- Rayon Billets
- OPAN carbon fabrics
- Fibers, non-woven textiles
- Composites
Facilities
- 100,000 ft² production facility
- 24/7/365 operations
- Furnace capability to 2,800°C
- Carbonization furnaces
- Continuous furnaces
- PVDC pyrolysis furnaces
- Chemical Vapor Infiltration furnaces
- Additional furnaces for production and development of ceramics, carbon, and other materials
- High performance needlers to process 3D carbon preforms
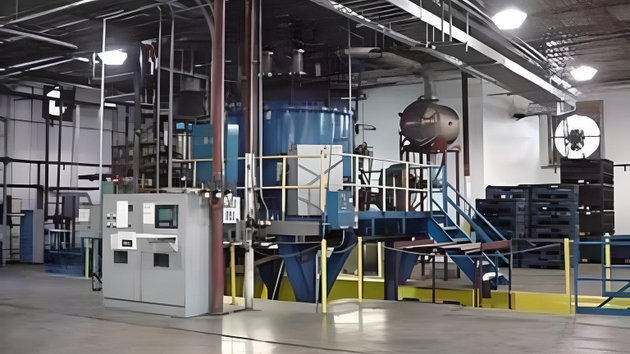
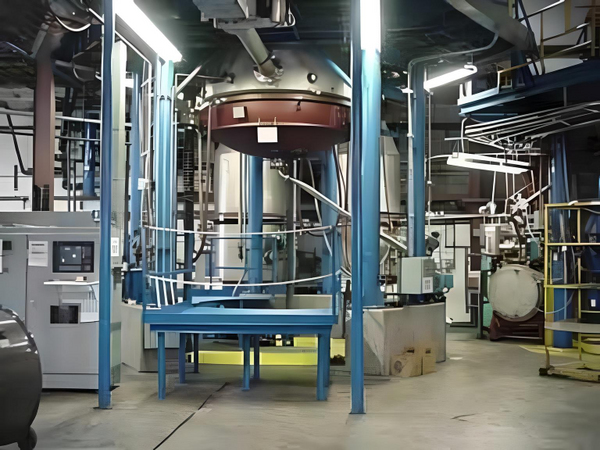
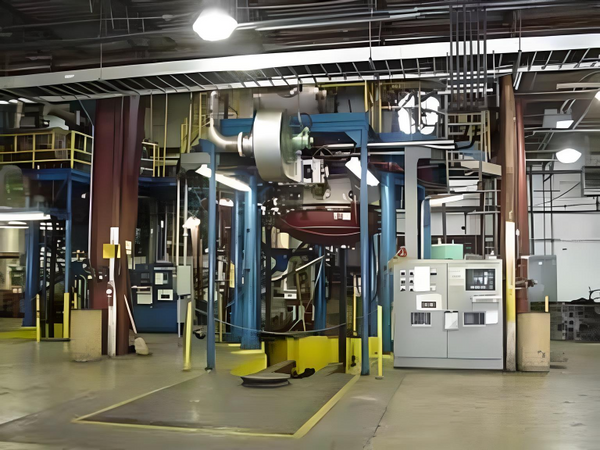
Quality
ISO 9001:2015 and AS-9100D Certified
- BAM’s ISO 9001:2015 and AS-9100D certifications are testaments to our dedication to maintaining the highest standards in quality management. These certifications ensure that our industrial and aerospace processes are meticulously controlled and consistently meet or exceed industry benchmarks. We are proud to uphold these rigorous standards in every aspect of our operations.
A Decade of Excellence
- At BAM, we are exceptionally proud to share that we have not encountered a single audit discrepancy in over 10 years. This remarkable achievement reflects our unwavering commitment to precision, consistency, and excellence. It is a testament to our stringent quality control measures and the dedication of our entire team.
Commitment to Continuous Improvement
- While our track record is impeccable. We believe in the relentless pursuit of improvement. BAM is committed to ongoing process enhancement to ensure that we remain at the forefront of quality and innovation. We continually invest in cutting-edge technology and training to deliver superior products to our valued customers.